Back when factories were powered mostly by steam and water, they surely couldn’t have imagined things would advance this far. But they certainly did, and these days many people in the field refer to the industry of those days at Industry 1.0. (Which certainly isn’t a term they used back then!) Then the manufacturing revolutions bolstered by electricity and brand new inventions. Some refer to this stage of industry as Industry 2.0. Industry 3.0 would see the use of IT and electronics to take automation to new levels.
So what exactly is Industry 4.0, if we’re going to follow the pattern? Good question. For the past couple of years, people in the field have been throwing this term around. This follows the boom of the importance of data. (This phenomenon is often referred to as big data.) This, of course, was bolstered by the rise of the Internet of Things.
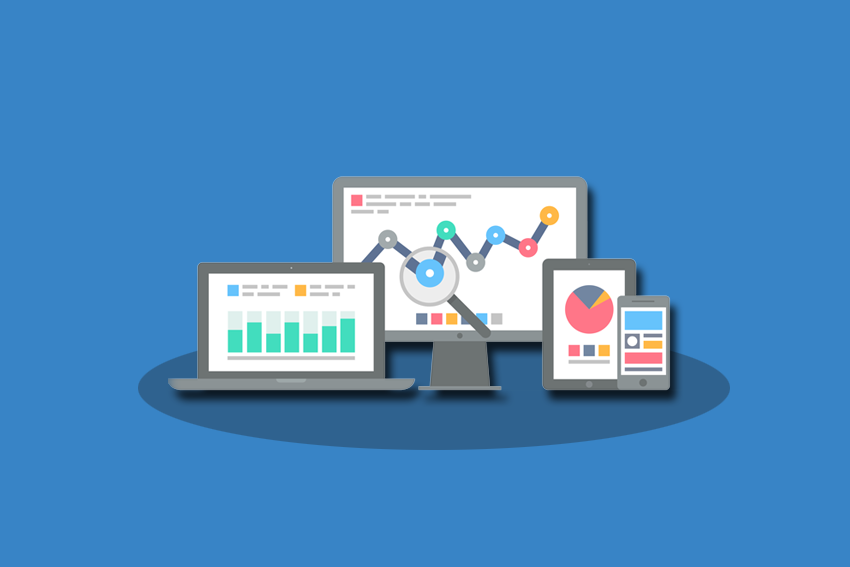
Data has always been pretty important to industry. After all, how could factories stand to be successful if they didn’t have their hands on certain data? They needed to follow demand, the accuracy of their process, sales, etc. But we’re now entering a whole new sphere of understanding when it comes to these things.
The modern appreciation of the importance of data doesn’t mean that everything is changing physically. Not everything is being completely overhauled by mind-boggling technology. After all, the logging and tracking of safety data is still best done in efficient, paper-based ways. MSDS sheets are still among the best ways of tracking data in industry. So it’s not that everything is being overhauled from a technological standpoint. Rather, we’re seeing changes in perspective. The Internet has given us a new and deeper appreciation of data.
That being said, technological advancements are still at the forefront of Industry 4.0. And the Internet of Things definitely has its place in this vanguard. Sensor technologies have made almost every element of the manufacturing process a potential ocean of data. This has been seen quite extensively in the car manufacturing industry. But pretty much every field in industry is discovering the benefits. Efficiency and yield increases have been seen with implementation of “data mining” during production. Even reduces in product defects have been seen with the increase in factory technology that uses the Internet of Things.
All of this information, of course, can lead to higher profits. By cutting waste in production materials, a decrease in the waste of money is only natural! But data mining also reveals exactly what it is the customers and clients want from this process. That, plus the use of social media, can help you finetune your quality management. (And if you didn’t think manufacturers could make much use of social media, think again! It’s an integral part of Industry 4.0.) The increased gathering of production data can help you automate quality assurance processes. Profits can go through the roof if you’re combining this correctly with the desires of consumers.
Make sure you don’t neglect data in your manufacturing process. Become one with Industry 4.0. And as soon as we start to hear whisperings of Industry 5.0, we’ll let you know!